Ingot molding and packaging line is aimed for aluminum ingots production of 20 kg and enables to provide the following automated process: metal molding, cooling and marking of ingots, layer-by-layer packaging, strapping and marking of packages.
Technical Parameters
Capacity, t/h
|
25
|
Ingot weight, kg
|
20±3%
|
Package weight, kg
|
Up to 1100 (54 ingots in package)
|
Product
|
Pure aluminum
|
Ambient temperature, °С
|
From 10 to 41
|
Liquid metal temperature at molding station, °С
|
From 700 to 740
|
Ingot temperature, °С
|
After primary cooling After secondary cooling <60
|
Capacity of ingot stacker, ingots/hour
|
1250 (nominal)
|
Noise level, dB (А)
|
Average value of 80 at working stations
|
Number of operators, persons
|
2 (for line) 1 (for forklift loader)
|
Molten primary aluminum extracted from electrolytic cells by means of vacuum ladle is fed into cast house for removing nonmetallic and gaseous impurities and further treatment into marketable pro-ducts (ingots). Before casting liquid aluminum is held in molten state in mixers.
Casting aluminum from the mixer into ingots of casting conveyor is performed by molding station. The molding station includes a chute with metal level control system, casting wheel and tilting ladle for aluminum dump in emergency case.
The casting wheel provides batch wise filling of molds with aluminum. Before filling the molds are prelubed and preheated. By moving through the casting conveyor ingots are forced cooled down to 400°С. At the end of the casting conveyor ingots are released from the molds and automatically put onto a secondary cooling conveyor.
During transportation through the secondary cooling conveyor ingots are forced cooled down to 60°С and marked.
Then the layer-by-layer stacker places individual ingots onto the storage table and turns them over for 180°, if required. A layer of ingots is formed on the storage table. The robot transfers the ingot layer onto a finished product conveyor.
A package of ingots in required quantity is formed on the conveyor. The conveyor moves the finished package to a package storage facility. During pa-ckage transportation through the conveyor it is strapped, weighed and marked. The storage facility is provided for temporary storage of up to 10 ingot packages. From the storage facility packages are transported to the finished products warehouse.
Ingot molding and packaging line consists of the following:
- Molding station (chute, metal level control system, tilting ladle, casting wheel)
- Casting conveyor
- Mold lubricator
- Mold and casting wheel heater
- Mold and ingot forced cooling system
- Ingots release station
- Ingot discharge system (placing onto the secondary cooling conveyor)
- Secondary cooling conveyor
- Secondary cooling device
- Marking device
- Layer-by-layer stacker
- Robot
- Finished product conveyor
- Strapping machine
- Weighing machine
- Package marking machine
- Storage facility for packages
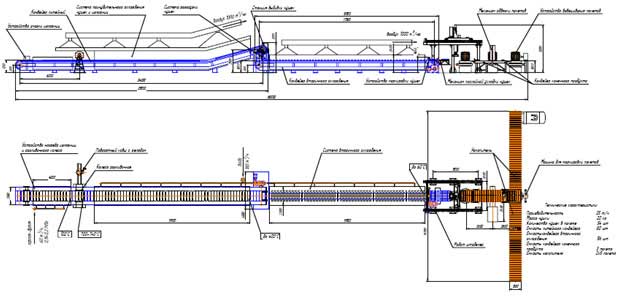