Data processing system based on IVK MicroTEK-01 for three metering stations with common checking line
|
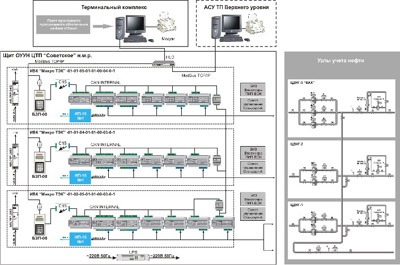
|
Facility: Metering Station
|
|
Meter run unit:
- turbine flow converter (TPR) - differential pressure transducer
|
Discharge manifold:
- pressure transducer - temperature transducer
|
Quality assurance unit(BKK):
- mixer - flow moisture meter - automatic sampler
|
Common checking line:
- turbine flow converter (TPR) - temperature transducer - pressure transducer
|
Functions:
-
collection and processing of information from primary converters for flow, density, humidity content, temperature, pressure and differential pressure
- automatic control, indication and warning of metered parameters limit values
- calculation, indication and transfer of recoded parameters to operator's work station (RSO) through Ethernet Modbus TCP/IP interface
- Supply of all primary converters hooked up to the system
- control over automatic samplers as per GOST 2517-85
- mode of metrological characteristics check (KMKh) with control turbine flow transducer and turbine flow transducer with mechanical displacement prover
- drawing up, storage and printing of control charts
- storage and printing of two-hour, shift, daily and monthly reports, archives and event and emergency logs
- uninterrupted power supply to system during two hours by central power supply cutoff
|
Features:
- check of metrological characteristics of all metering stations with general control line
- general operator's work station (RSO) based on InTouch software applications package
|
Data processing system based on IVK MicroTEK-01 for metering station, gas and water metering stations
|
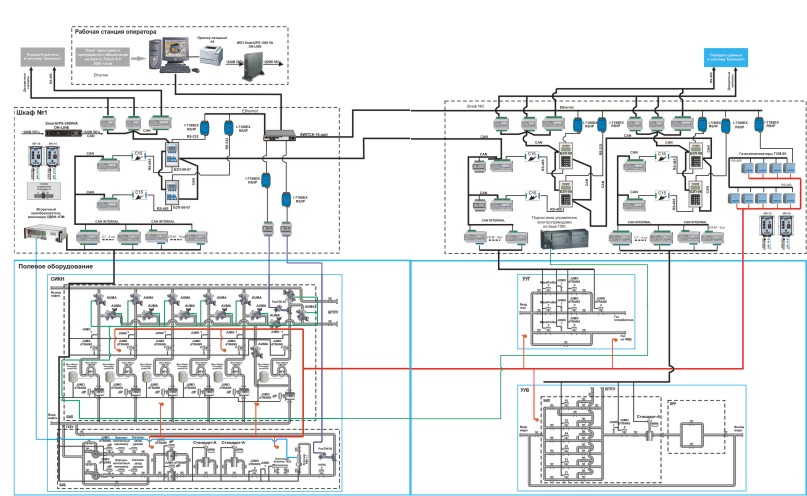
|
Facility: Metering Station
|
Facility: Gas Metering Station
|
Meter run unit (six MR):
- mass flow converter (PMR) - 6 pcs. - differential pressure transducer on filter - 6 pcs. - pressure transducer - 6 pcs. - temperature transducer - 6 pcs. - ball valve with electric drive - 20 pcs.
|
Meter run unit (three MR):
- mass flow converter (PMR) - 3 pcs. - pressure transducer - 4 pcs. - temperature transducer - 3 pcs. - ball valve with electric drive - 2 pcs.
|
Discharge manifold:
- pressure transducer - 1 pcs. - temperature transducer - 1 pcs. - control valve with RemTEK-02 electric drive - 1 pcs.
|
Facility: Water Metering Station
|
Quality assurance unit (BKK):
- turbine flow converter (TPR) - 1 pcs. - pump - 2 pcs. - pressure difference transducer on pump - 2 pcs. - electric-contact manometer - 2 pcs. - ultrasonic alarm device - 2 pcs. - pressure difference transducer on filter - 1 pcs. - automatic sampler - 1 pcs. - pressure transducer - 1 pcs. - temperature transducer - 1 pcs. - flow humidity meter - 1 pcs. - flow densitometer - 1 pcs.
|
Meter run unit(six MR):
- ultrasonic flow converter - 6 pcs. - pressure transducer - 1 pcs. - temperature transducer - 1 pcs. - automatic sampler - 1 pcs.
|
Flow control unit:
- pressure transducer - 1 pcs. - temperature transducer - 1 pcs. - ball valve with electric drive - 2 pcs.
|
Functions:
- collection and processing of information from primary flow transducers for mass, temperature, pressure and differential pressure, humidity and density
- control over ventilation by means of GSM-05 gas detectors digital outputs by elevated concentration of burning gases (actuation of threshold 1 and 2)
- calculation, indication and transfer of recoded parameters to operator's work station through Ethernet Modbus TCP/IP interface and to "Teleskop+" telemechanics system through RS-485 Modbus RTU interface
- supply to all primary converters hooked up to the system
- control over automatic samplers as per GOST 2517-85
- uninterrupted power supply to system during two hours by central power supply cutoff
- calibration and check-out modes for metrological characteristics (KMKh) of volume and mass flow converters with reference flow meter and calibration rig, drawing up and printing of KMKh and calibration reports
- Drawing up, storage and printing of two-hour, shift, daily and monthly reports, archives and event and emergency logs
- supply disconnection to instrumentation transducers located on metering stations by external fire-fighting system actuation
- control over pumps of quality assurance unit from operator's working station
- flow control through meter run unit from RSO by means of control over RemTEK-02 electric drives
- control over AUMA electric drives for stop valves by means of digital signals (24 V)
|
Features:
- Hot reservation of computers and parameters display units for UUN, UUG and UUV
|
AIS Khozuchet power resources metering system based on IVKMicroTEK-04 for high-pressure polyethylene (PEVD) manufacturing
|
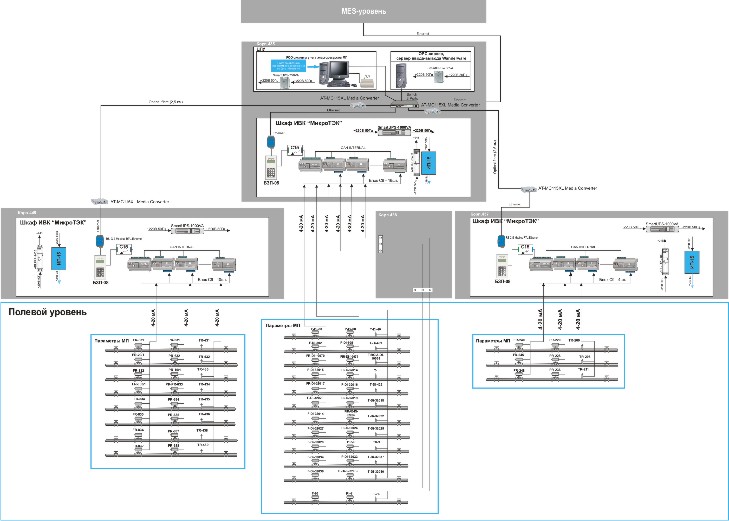 |
Automation Object:
PEVD manufacturing automation object is a set of pipelines of accounting flows of the following facilities:
- workshop # 408 - polyethylene manufacturing - workshop # 409 - polyethylene manufacturing - workshop # 410 - polyethylene manufacturing - workshop # 411 - manufacturing of polyethylene and technical carbon based materials
Total amount of routine metered material flows of all workshops is 31.
|
Functions:
- collection and processing of information from differential pressure and temperature transducers
- automatic control, indication and warning of limit values of metered parameters
- nulling of cumulative counter on operator's signal
- Drawing up, storage and printing of hourly, shift, and daily reports and archives
- measurement, calculation, indication and delivering parameters to RSO which are necessary for gas and liquid metering
- system time correction particularly by means of higher level software as per Modbus RTU protocol
- diagnostics and indication of field equipment operability
- system information protection from illegal access using passwords and lock words
- data transfer to MES-level system of PEVD manufacturing through Ethernet network
- manual input of physico-chemical parameters of power resources
|
Features:
- distributed metering system over facility territory open-ended and redundable
- fibre-optic communication lines for RSO and IVK MicroТEК of distant facilities of workshops # 408 and #409
- centralized visualization system (RSO) providing real time access to changeable parameters and collected archives
|